
Glitter Distribution Unit for Rotary Printing – mod. TDP
Technical Features
Glitter Distribution Unit for Rotary Printing – mod. TDP
The Glitter Distribution Unit mod. TDP consists of one hopper containing glitter, with an inverter controlled dosing cylinder of adjustable speed placed at its base. A doctor blade opposed to the cylinder is used to adjust the glitter output. A rotating brush is mounted opposite to the cylinder and is used to remove the glitter and distribute it onto the fabric underneath. Brush speed is variable and controlled by an inverter. The unit can be inspected through Plexiglas panels.
The unit is completed with:
– Electrostatic Dispersion Unit mod. GDE, consisting of one insulated structure for the electrostatic field and one electrostatic generator with adjustable tension from 0 to 50 kV, used to improve glitter distribution uniformity.
– Suction System mod. BB1, consisting of a suction blade placed at the glitter distributor exit. Vertical adjustment for the gap between the blade and the conveyor belt is provided. The blade is connected to a fan equipped with filtering sleeves and a collecting bag for the recovered glitter.
– Brushing Unit mod. SZ1 is placed at the oven outlet and consists of:
- One rotary brush motorized at a fixed speed. The pressure of the brush against the counter roller is adjustable through an electric motor
- A fan with filtering sleeves and a collecting bag to be connected to the brush deck for the recovery of removed flock
The Glitter Distribution Unit can be used alone or combined with a Flocking Group mod. TC2 (see scheme below).
Our glitter distribution units can also be installed at the entrance of coating lines between the coating head (with blade and/or rotary screen printing) and the oven.
Their reduced size and their easy installation allows for the tooling up of the printing and coating lines in order to create added value on fabrics, paper, etc.
For the coating lines these units are equipped with collectors for glitter excess recovery, connected to a suction system and a possible recirculation system. Groups of beater bars can also be installed, similar to those already employed in the flocking machines, which give a more uniform glitter distribution on the surface.
Our units ensure high standards of quality, repeatability of the product and easy maintenance.
Technical data
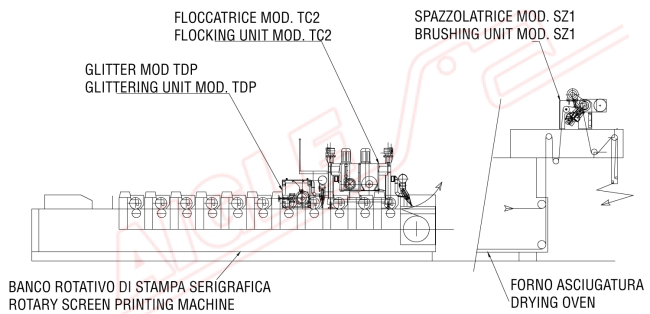